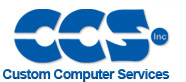 |
 |
View previous topic :: View next topic |
Author |
Message |
varadharaj
Joined: 09 Apr 2012 Posts: 19 Location: Salem
|
Reg: PWM splitting |
Posted: Thu Oct 10, 2013 12:20 am |
|
|
Hi,
I am using pic16f877a for speed control of dc motor which is taking 60v and 1500 watt max. So i planned to split the load to different mosfets(max 8).
Can i use one pwm from microcontroller and control 8 mosfets?
Thanks, _________________ Embedding Innovation |
|
 |
temtronic
Joined: 01 Jul 2010 Posts: 9246 Location: Greensville,Ontario
|
|
Posted: Thu Oct 10, 2013 5:28 am |
|
|
Yes...but we need more inforamtion.
From your question, I think you want to just control the speed, in one direction of that motor(classic PWM). If so, then the 8 MOSFets can be run in 'parallel' with a small gate resistor in each.Just check the datasheet for the device you're using. This is how hobby RC ESC units are built.Typically the gate resistor is 47-100r.
You could also do it using 1 MOSFet. 1500W/60V = 25Amps. Lots of MOSFets will handle that power/Voltage/current , and split between 8 devices, that's only 3 1/2 amps each. Just be sure to properly heatsink the devices !!
If this is what you want, then you only need ONE pin for the job !!
hth
jay |
|
 |
Mike Walne
Joined: 19 Feb 2004 Posts: 1785 Location: Boston Spa UK
|
|
Posted: Thu Oct 10, 2013 12:58 pm |
|
|
I would add:-
1) Carefully check your FET's gate threshold voltage.
2) What is your PWM frequency?
3) Have a close look at the PIC's PWM waveform.
4) You can use ferrite beads in place of the gate resistors.
5) What happens to your FET drain source voltage when the FETs turn off?
Mike |
|
 |
varadharaj
Joined: 09 Apr 2012 Posts: 19 Location: Salem
|
|
Posted: Thu Oct 10, 2013 11:17 pm |
|
|
Hi,
thanks for your replies.
@temtronic, yes, exactly, i need the motor to be controlled in only one direction. So, can i use the gate resistor in each FET's gate ? Can i able to connect the gate resistor directly to the microcontroller PWM output pin?
Thanks _________________ Embedding Innovation |
|
 |
Mike Walne
Joined: 19 Feb 2004 Posts: 1785 Location: Boston Spa UK
|
|
Posted: Fri Oct 11, 2013 2:56 am |
|
|
Quote: | So, can i use the gate resistor in each FET's gate ? | Yes, it's important you use a resistor (or similar) to each FET gate.
Quote: | Can i able to connect the gate resistor directly to the microcontroller PWM output pin | Yes, with reservations.
You're still not telling us enough, to help you properly.
Mike |
|
 |
Ttelmah
Joined: 11 Mar 2010 Posts: 19552
|
|
Posted: Fri Oct 11, 2013 4:11 am |
|
|
There are so many parts to this that need you to do a lot more research:
FET's have significant input capacitance. Depending on the switching speed required, it may require several _amps_ to be momentarily delivered to the gate to charge/discharge this capacitance in the time required. The PIC output can only deliver 25mA....
Then you are assuming that the gate only needs something under 5v to drive it. Most FET's require a gate voltage well over the (nominal - really a lot less than this) 5v, the PIC can deliver. Using 'logic' MOSFET's, often involves more expense, than using a proper driver.
These are Mike's "reservations"...
You may well want to switch 'asymmetrically', with faster discharge times than charge times, making the drive network to the gate more complex.
The gate resistors, or more complex circuit, if designed 'right', help to control parasitic oscillations that can otherwise result from the slight imbalances in both devices, and layouts.
Faster switching, gives better efficiency, with the FET spending less time 'part on', but then increases potential noise problems. Both need to be considered.
People have mentioned good heat-sinking. One critical part of this is good heat _coupling_ between the devices. Not only must they all be kept cool, but they must be kept at the same temperature. Careful design here is vital.
You talk about driving a motor. Don't rely on the internal diodes in the FET as your trap diodes, unless you spend 'extra' and buy FET's that are specifically designed to be used this way. Generally you will get better efficiency using a separate trap diode, and even better using another FET as the trap device.
Your power level is quite low, but have you considered what happens during initial acceleration, in your '1500W' figure?. The currents drawn at start, need to be considered.
Part of keeping everything balanced, is also careful design of the board itself. Don't start out with bits of wire, and expect things to behave correctly...
Best Wishes |
|
 |
Mike Walne
Joined: 19 Feb 2004 Posts: 1785 Location: Boston Spa UK
|
|
Posted: Fri Oct 11, 2013 10:45 am |
|
|
You should be realising by now, this is far from being a trivial task.
1) When the FETs turn off, it's likely one FET only will break down in avalanche mode. Is this a problem?
2) How long is the lead to your motor?
3) Are you proposing using any RF suppression?
4) What happens if/when the motor stalls?
We've only just started to scratch the surface!
You risk creating a lot of expensive smoke.
After the fire, don't complain you were not warned.
Mike |
|
 |
temtronic
Joined: 01 Jul 2010 Posts: 9246 Location: Greensville,Ontario
|
|
Posted: Fri Oct 11, 2013 1:21 pm |
|
|
If you want an easy, hassle free solution, just buy an RC ESC. Check the specs but some will easily do the job.
All you then need to code is the RC servo code on the PIC ,again a trivial few lines.
This will save you days of burning the midnight oil, trying to get your 'homebuilt' motor section working properly.
just another way of doing it
Jay |
|
 |
Ttelmah
Joined: 11 Mar 2010 Posts: 19552
|
|
Posted: Fri Oct 11, 2013 2:05 pm |
|
|
Yes. Just make sure you look for the 'HV' types. Most standard ones are limited to perhaps 48v.
and, just expand a bit further, most 'ESC' units on sale now are for brushless motors. Since the original poster appears to be talking about a brushed motor, be careful to get the right type.
There are also similar controllers for 'ebikes', again with both brushed and brushless designs available, and quite a few of the Chinese units support this type of power level. Generally most designs tend to stop at a nominal 48v - this is because the safety regulations change at this voltage - beware of this, if the 'nominal' voltage is over 50v, you switch to having to meet higher insulation standards. However 'nominal' is the key word, with 48v 'ebikes' using batteries that will deliver about 56v fresh from the charger.....
The ebike controllers, once you turn off things like pedal/brake sensing, just require 0 to 5v as an input to control the speed.
Best Wishes |
|
 |
varadharaj
Joined: 09 Apr 2012 Posts: 19 Location: Salem
|
|
Posted: Sun Oct 13, 2013 8:06 pm |
|
|
Hi,
My application is for electric vehicle. The supply voltage of motor is 60 and the normal working current is 25A..The initial current is about 100A. Using Pwm, i need to control the speed of the motor.. No forward and reverse direction control.. We change it manually..
Thanks.. _________________ Embedding Innovation |
|
 |
temtronic
Joined: 01 Jul 2010 Posts: 9246 Location: Greensville,Ontario
|
|
Posted: Sun Oct 13, 2013 8:45 pm |
|
|
The design of the PWM 'controller' requires specific knowledge of the motor's characteristics. Obvious ones are voltage, run current, FLA, frequency of operation( Hz or KHz ?). Needing 100A means special board layouts, EMI concerns,interconnections, etc.
This is NOT an easy task, even after 30 years of R&D, I'd buy an 'off the shelf' solution for far less money than several weeks of design, test, poof, redesign, retest, poof, then buy a ready made product.
As previously posted, off shore products are easy to modify, cheap and simple to use.
If you want to try ....then ..as for discrete or chip devices, try IR (International Rectifier Corp.) for devices and appnotes.
hth
jay |
|
 |
Ttelmah
Joined: 11 Mar 2010 Posts: 19552
|
|
Posted: Mon Oct 14, 2013 1:19 am |
|
|
as another comment, if this is for a vehicle, are you really 'sure' you want to be using a brushed motor?.
I can't think of any vehicle drive system designed in the last ten years that went brushed. Brushless have better efficiencies, and this is normally 'key'.
Also since in a vehicle application, you _will_ need to detect if the motor is stalled, and limit current in this situation, a hall effect sensor brushless motor solves a lot of problems.
If you are committed to 'brushed', look at the derivatives of electric golf cart controllers. People like Curtis Wright, do 'conventional' brushed motor controllers, with the smaller models used for golf carts, and larger versions for things like fork-lift trucks (though the newer versions of these are now brushless).
Back though to have you looked at the legal requirements of your voltage?. If the peak voltage in the circuit exceeds 60v, you switch to having to use higher insulation and protection standards (unless the current is inherently very limited). Beware.
Best Wishes |
|
 |
|
|
You cannot post new topics in this forum You cannot reply to topics in this forum You cannot edit your posts in this forum You cannot delete your posts in this forum You cannot vote in polls in this forum
|
Powered by phpBB © 2001, 2005 phpBB Group
|