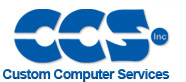 |
 |
View previous topic :: View next topic |
Author |
Message |
Zek_De
Joined: 13 Aug 2016 Posts: 100
|
Full-Bridge problem |
Posted: Wed Dec 21, 2016 4:03 am |
|
|
Hello friends,
I'm making a full bridge to drive DC motor but I have a problem.
Voltage on motor is not 12V that I feed mosfets with 12V, on motor is like 8.6V. At the same time the voltage that I got from source, I'm giving to feed mosfet. I mean voltage to motor is 12V, to mosfet 12V, but voltage for the mosfet should be 20V. That mosfet is finally in saturation and short-circuit and all current is free.
My question is how can I get 20V that is mustnt finish power, because in my way when I got 20V for exampe with 555, when I didn't send power the mosfet, 20V pull ground and my stored energy is 0 and to full again want to time.
Also second one, push-pull is useless to drive a mosfet because of voltage problem for example when I feed push-pull with 12V and I give high for transistor, output is not 12V and mosfet don't work good and result less voltage on motor.
Like this
https://www.google.com.tr/url?sa=i&rct=j&q=&esrc=s&source=images&cd=&ved=0ahUKEwiN4dCni4XRAhUGXRQKHRn7CPEQjRwIBw&url=https%3A%2F%2Fmycontraption.com%2Fhigh-power-mosfet-motor-driver%2F&bvm=bv.142059868,d.ZGg&psig=AFQjCNEPMZ4Rjfw5EgdV6Ea5AM2vFkys3A&ust=1482402900981619 |
|
 |
Ttelmah
Joined: 11 Mar 2010 Posts: 19549
|
|
Posted: Wed Dec 21, 2016 4:49 am |
|
|
This is not really the forum for this question. Nothing at all to do with CCS C....
For more questions like this you really need to go to a basic electronics forum.
However first, you won't get the full voltage. Everything has some droop. A well driven FET though, can have drops that are only a tiny fraction of a volt.
Key though is 'well driven'. N channel FETs are inherently slightly more efficient than P channel types. This is why power bridges will commonly use four N channel devices. A N channel FET connected as the high side driver, requires it's gate to be taken to above the high side drive voltage. So you have to generate a supply rail 'above' the positive supply to drive the upper FETs.
Look at:
<http://www.armory.com/~rstevew/Public/Motors/H-Bridges/Blanchard/nch-brdg.htm>
Now also for efficiency, you may be surprised at just how much current the devices driving the FETs will have to deliver. The inputs of a FET are 'voltage controlled', but they have a huge capacitance (typically several thousand pF on a power FET, and more if you parallel FETs for even lower on resistances). To change the voltage quickly from 'off' to 'on', therefore requires a momentary high current. Look at proprietary driver IC's designed to drive a pair of FETs (which also includes the inverter to generate the high side gate voltage), like:
<http://www.onsemi.com/PowerSolutions/product.do?id=NCP5181>
Devices like this can deliver over an amp to switch the gate.
I'd suspect you are trying to drive N channel FETs from a voltage near to the supply, so the upper FETs are only giving an output Vgs below this.
Have a look in here:
<http://www.electro-tech-online.com/>
Look at the section on "PIC micro tips & tricks for DC motor control". |
|
 |
Zek_De
Joined: 13 Aug 2016 Posts: 100
|
|
Posted: Wed Dec 21, 2016 5:06 am |
|
|
Okay, thank you for websites Ttelmah. |
|
 |
temtronic
Joined: 01 Jul 2010 Posts: 9245 Location: Greensville,Ontario
|
|
Posted: Wed Dec 21, 2016 8:16 am |
|
|
Depending on your application, have a look at RC ESC modules.
These are the Electronic Speed Control modules that the Radio Control guys use to interface their receivers to motors. It might work for you?
Simple to interface as PIC just needs to send a signal to ESC, the ESC has all the power FETs, logic to do the rest !
Jay |
|
 |
Zek_De
Joined: 13 Aug 2016 Posts: 100
|
|
Posted: Wed Dec 21, 2016 8:55 am |
|
|
Thanks Jay, these websites my answers, now I can do a good driver. |
|
 |
Ttelmah
Joined: 11 Mar 2010 Posts: 19549
|
|
Posted: Wed Dec 21, 2016 8:55 am |
|
|
Also, as another driver that is often 'forgotten', the ESC units for ebikes.
Some of these have a 'reverse' option (usually just a connection, that is left open or made), and ones are available that control DC motors or BLDC motors. The input is usually just a DC voltage 0 to just under 5v (easy to synthesise with a PWM. Price wise, they often cost less than the FETs they contain!... |
|
 |
Zek_De
Joined: 13 Aug 2016 Posts: 100
|
|
Posted: Wed Dec 21, 2016 4:01 pm |
|
|
I don't know how to work ESC, is this control motor speed itself or I have to control with software ? Do you know a website about for this ? Also websites that you say is perfect, I made circuit. |
|
 |
Ttelmah
Joined: 11 Mar 2010 Posts: 19549
|
|
Posted: Thu Dec 22, 2016 2:15 am |
|
|
'ESC' is electronic speed control.
The RC ones take a pulse between 1mSec, and 2mSec to give 'off' to 'full'. The more sophisticated ones are themselves programmable, so you (with a suitable cable), can program them so that (say) the 'off' pulse gives 50RPM, while the 'full' is 2000RPM. On these 'smart' ones, you can program how fast they will accelerate, maximum current, and even whether they produce a particular revs, or a 'torque' for the incoming pulse width. Once setup, a pulse of 1mSec says 'generate 1000rpm', and they will do it. The neat thing is that they will keep producing this till the next pulse (many have a 'cutoff' so if a pulse is not seen for perhaps a second, they assume something has gone wrong and stop - radio failure stop). However provided a pulse is sent at reasonable intervals they keep producing the revs/power you have told them to generate.
There are two fundamentally different types. Ones for cars have 'forward/reverse', while ones for helicopters/planes are 'forward' only.
Because they are mass produced, the prices are way below what you could make them for. For instance:
<https://hobbyking.com/en_us/hobbykingr-tm-brushless-car-esc-30a-w-reverse.html>
The link on the page there goes to a cheap programmer that allows you to set the current etc..
Now, just the FETs on that unit would cost about 4* what the unit costs, and it has temperature shutdown, overcurrent shutdown etc...
It even has a built in 5v regulator designed to run the radio.
They are 'smart' and treat the first pulse seen (if stable) after power 'on' as the 'zero' point.
The bike ones, take a DC voltage. 0v = stop, up to about 4.2v for full speed. Again most are programmable, and again the programmer is an extra item.
Thing is that if you are getting involved in trying to control DC motors at reasonable power, board layout becomes really important. Typically you'll need thicker copper than standard boards, multi layer design with a ground plane, and often some quite awkward layout features (for SM FETs, pads with several holes linking them to specified areas inside the board etc..) These boards have been built, and already tested.
On the same site, there are units rated to give 150A continuous and handle over 1000A momentarily (these handle motors up to about 4HP on 22v supplies!....).
Now the one I point to there is for a BLDC motor, not a 'brushed' motor. Most people these days would use BLDC. However ones to drive brushed motors are available, though much harder to find. |
|
 |
temtronic
Joined: 01 Jul 2010 Posts: 9245 Location: Greensville,Ontario
|
|
Posted: Thu Dec 22, 2016 5:48 am |
|
|
Mr T's comments on the Ebike ESC is correct ! There seems to be an 'Industry standard' set of connectors which helps and I've seen some good for 1000W of power for sale for $20 USD! I can't even buy the nice,extruded aluminum case for that!!
I've been doing this PICstuff for 30+ years and wouldn't think about making my own power section for a 'motor controller'. As Mr T points out there is a LOT of hard engineering/design tht you MUST do to get it right AND reliable. It's far better use of your time to spend a few dollars more for a premade controller and concentrate on the 'main' code of your project,than spending weeks trying to find out why the SMT PCB keeps burning up.....
Jay |
|
 |
Zek_De
Joined: 13 Aug 2016 Posts: 100
|
|
Posted: Thu Dec 22, 2016 9:37 am |
|
|
Okay friends ,thanks for informations |
|
 |
|
|
You cannot post new topics in this forum You cannot reply to topics in this forum You cannot edit your posts in this forum You cannot delete your posts in this forum You cannot vote in polls in this forum
|
Powered by phpBB © 2001, 2005 phpBB Group
|