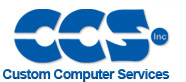 |
 |
View previous topic :: View next topic |
Author |
Message |
artohautala
Joined: 17 Nov 2011 Posts: 187
|
servo control |
Posted: Tue Jun 26, 2018 6:42 am |
|
|
Hello,
I want control servo "standard" 50 Hz frequency...
My code works well with 50 % duty cycle but frequency is far too
high. It's about 1.49 kHz. It should be 50 Hz.
Please help me to get PWM control for 50 Hz.
all the best for you all
Code: |
#include<18F452.h>
//#include <string.h>
#fuses HS,NOLVP,NOWDT,PUT
//#FUSES H4 //This is HS, with 4* PLL - H4 config bit.....
//#use delay(clock=8M)
#use delay(clock=8000000)
//************************************************************************************************
void main(void){
while(1){
// C1 = pin 16 = CCP2, C2 = pin 17 = CCP1
setup_timer_2(T2_DIV_BY_16, 255, 16); //this is for PWM 1 & PWM 2
setup_ccp1(CCP_PWM); // Configure CCP1 as a PWM
set_pwm1_duty(127);
stop:
;
goto stop;
}
}
|
|
|
 |
Ttelmah
Joined: 11 Mar 2010 Posts: 19552
|
|
Posted: Tue Jun 26, 2018 7:03 am |
|
|
Look in the code library.
There are multiple examples there of how to control servos.
The PWM is _not_ normally the way. Problem is if you wanted 50Hz, you would need to program the PWM to give 50Hz. Then the resolution would be very low.
If fact though 'high speed' servo update algorithms use 400Hz, not 50Hz. The actual 'update rate' for servos does not matter at all. You can leave most servos for several seconds without an update. Or update then at much higher rates. Only the pulse width actually matters. The reason for '50Hz', was that old radio systems used a 'frame' of pulses sent one after the other. The first pulse was for the first servo, the second for the second etc.. The whole frame usually comprised perhaps ten servo pulses, and then a pause to allow the internal counter to synchronise. The radio had simple logic that looked for the pause, and then gated the first pulse to the first servo, etc.. Modern digital radios no longer do this, and these will often simply send pulses to each servo at 400Hz. |
|
 |
temtronic
Joined: 01 Jul 2010 Posts: 9246 Location: Greensville,Ontario
|
|
Posted: Tue Jun 26, 2018 8:39 am |
|
|
yeesh, sad thing is I have some of the original RC servo chips that Signetics made in the mid 70s(?) in a drawer here....wonder if there's a market for them  |
|
 |
blowtorch
Joined: 11 Jun 2013 Posts: 35 Location: Cape Town
|
|
Posted: Thu Jun 28, 2018 3:15 am |
|
|
Some time back I had a project where I needed to occasionally drive a servo to a preset position (open / closed). The mechanical situation was such that the open position did not exert any force on the servo, but the closed position did. So I ensured that in the closed position the mechanical alignment would put the forces in a straight line, and therefore not "load" the servo. Therefore, after having arrived at either of the 2 preset conditions, I simply stopped sending pulses to the servo.
This code ran fine at a clock speed of 4MHz. Note the resolution was poor, but for my needs perfectly adequate given that I only needed an open / closed position. It was a very simple but effective approach that has worked for years.
Posted here in case it helps...
Code: | #define SERVO_OPEN 44 // used to set servo position1 via pwm2 duty
#define SERVO_CLOSED 134 // used to set servo position2 via pwm2 duty
void do_servo(uint16 servo_pos) {
setup_ccp2(CCP_PWM); // set CCP2 to PWM mode
setup_timer_2(T2_DIV_BY_64,255,1); //
set_pwm2_duty(servo_pos);
delay_ms(1500); // allow 1.5 seconds for servo to move into position
set_pwm2_duty(0L); // specific sequence to shut down PWM in low position
delay_ms(25);
setup_ccp2(CCP_OFF); // turn off the PWM...
output_low(SERVO); // ensure the PWM line low, probably not required
setup_timer_2(T2_DISABLED,255,1); // turn off the timer...save power
} |
|
|
 |
|
|
You cannot post new topics in this forum You cannot reply to topics in this forum You cannot edit your posts in this forum You cannot delete your posts in this forum You cannot vote in polls in this forum
|
Powered by phpBB © 2001, 2005 phpBB Group
|